Like many people, we have had the broken U-bolt experience. Our trailer U-bolt incident didn’t result in an accident, just temporary axle misalignment, but other people have been less fortunate.
For a start and what most people don’t realise is U-bolts are not reusable. Correctly designed and made U-bolts are cold-formed, with rolled threads and fitted with cut-thread nuts. This combination of thread and nut is designed to bind tightly when torqued, but slight deformation of the threads occurs during the torquing process. This surface alteration means that if U-bolt nuts are slackened off and retightened they will not reproduce the originally-designed clamping force, even if a tension wrench indicates correct torque level.
Another complication with U-bolts is their vulnerability to corrosion and damage. All U-bolts suffer from surface corrosion because of their position close to the road in all weather and temperature conditions. Also, many 4WDs and trailers have U-bolts with nuts fitted below the axle, so the threads can be damaged on rocky trails.
Removing nuts over corroded or damaged threads distorts the nut and the U-bolt threads, making re-use a very risky operation. Once U-bolts and nuts have been tightened they should be re-tensioned after the spring and the U-bolts have ‘settled’. However, if there’s any sign of damage or cracking they should be discarded and replaced by new U-bolts and nuts, which aren’t expensive. And remember, if one U-bolt on an axle needs replacement all four should be replaced, because a loss of clamping force on one side of the axle will cause stress on the other side as well.
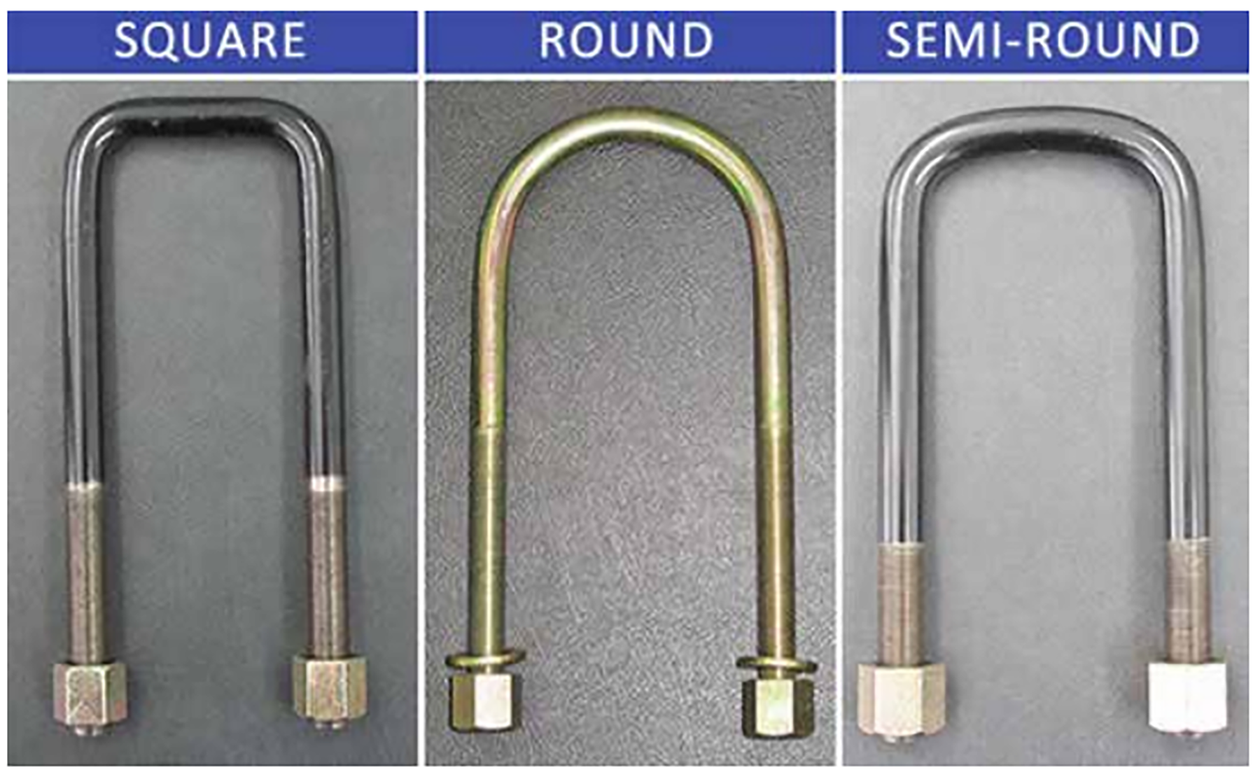
Corrosion and Cracking Issues
Many people ask why U-bolts aren’t made of corrosion-resistant materials, such as stainless steel. The answer is that exotic steel alloys and hardened steels are more prone to corrosion cracking and breaking than the milder steels used in most U-bolts. Also, U-bolts that have been heat-treated, heat-bent, welded, electro-plated or galvanised can be more susceptible to embrittlement than untreated U-bolts, unless they're correctly manufactured.
Unfortunately, there's no Australian Standard for U-bolt production and testing, so be sure to buy replacements from a reputable outlet. We’ve even had reputable reports of some imported, zinc-plated U-bolts that could be broken by hand!
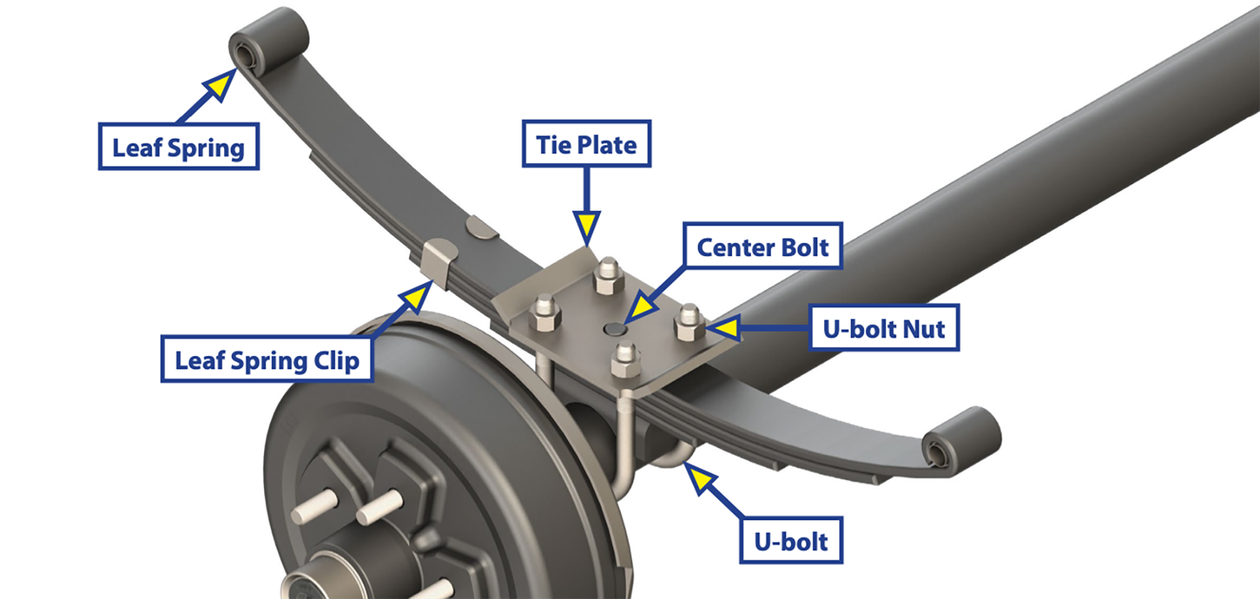
U-bolts should be designed with sufficient strength to clamp a spring pack for a life of thousands of kilometres, but, like all suspension components, they’re not ever-lasting. Every time the spring flexes, the U-bolt's clamping force restrains the axle’s natural tendency to depart from the spring. The resulting fatigue and weakening caused by corrosion eventually take their toll.
When fitting a replacement U-bolt it’s essential the profile exactly matches the axle profile or the profile of the adaptor plate that it fits over. This is particularly important if a generic U-bolt is fitted, rather than an original equipment bolt. A square-profile U-bolt must match the axle shape precisely, with minimal gap between the bolt’s three contact faces and the axle tube. Curved-profile U-bolts must also have a radius that mates evenly on the axle tube or the adaptor bracket, with no air gap between. A U-bolt that contacts the axle or adaptor at only a couple of high points will almost certainly suffer from cracking failure.
Regular U-bolt checks – every time the vehicle is on a hoist for routine maintenance – should include inspection of condition and tightness. Loose U-bolts rapidly lead to failure of one or more bolts and spring cracking, with total suspension failure and an accident then a certainty. When it comes to U-bolts – if in doubt, chuck ‘em out!